- Products
- Your Business
- Newsroom
- Tools & Resources
- About us
- CSR
- People & Careers
- Search
- Contact us
- Compare
- Sign in
Keep employees safe and healthy
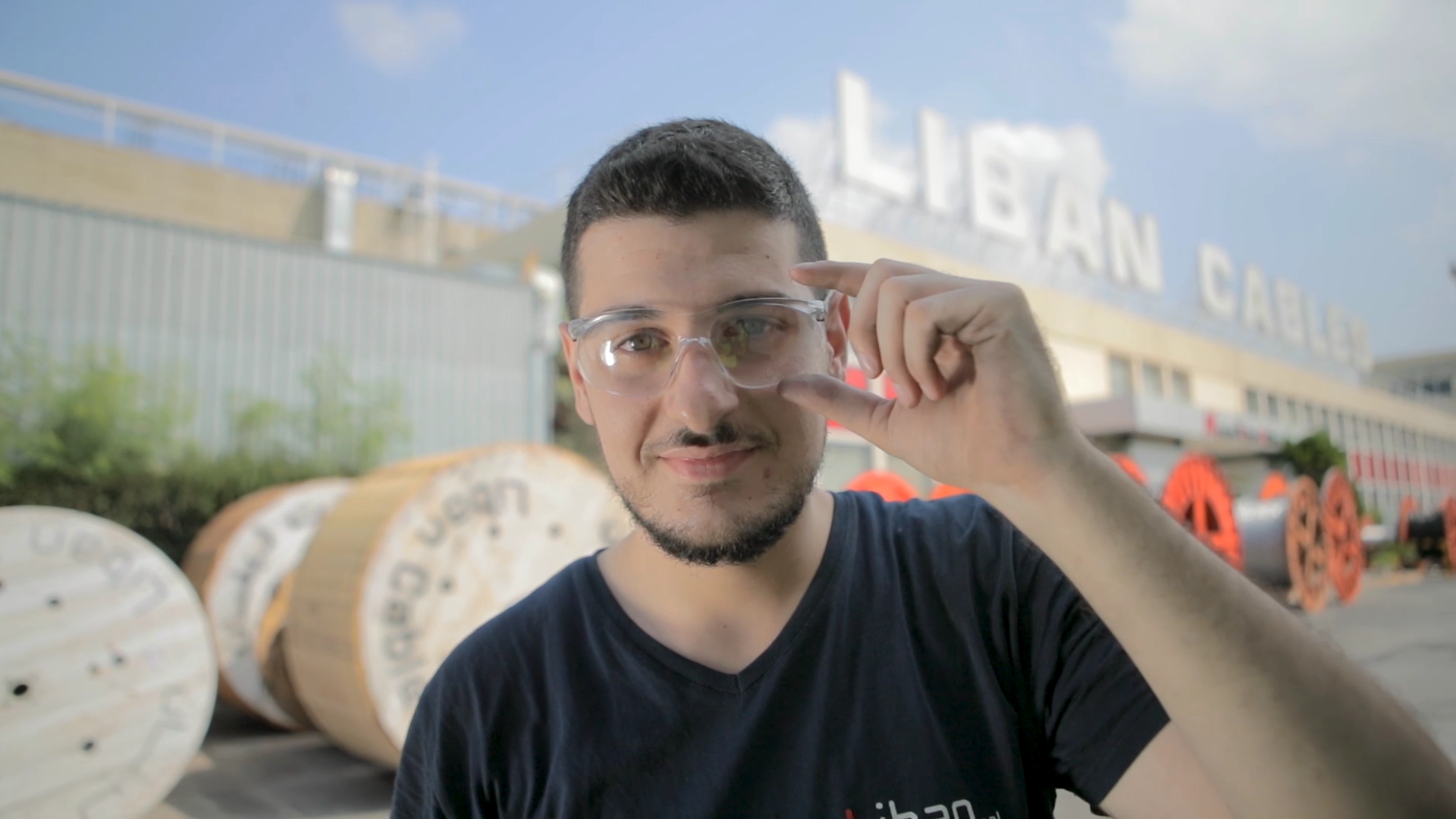
At Nexans, decision-making at the highest and most local level is inspired by the motto “SAFETY FIRST! Think Safe, Act Safe, Be Safe”. The health and safety of Nexans employees and partners - including subcontractors, temporary staff and customers - is a priority that has been transformed into a key performance indicator in the Group’s CSR policy.
To further reduce and prevent risk, in 2009, Nexans launched a workplace health and safety improvement program with the aim of reducing the workplace accident frequency rate by 30% each year.
To support this ambition, the Company set up a dedicated Health and Safety Unit reporting to the Industrial Management Department. A network of HSE representatives develop and implement health and safety standards and related initiatives covering technical aspects (e.g. handling of cable drums and electric testing), methodology (maintenance rules and consignment) and behavior.
Workplace safety
The Group has put in place the following programs and initiatives:
Basic Safety Tools
Supported by our HSE and Continuous Improvement teams, employees use standard safety resources on a daily basis:
- Job Safety Analysis (JSA): analyze tasks performed, identify exposure risks and determine corrective measures
- Safe and Un-Safe Act (SUSA): report safety problems and suggestions
- Safety Proactivity: calculate performance criteria by monitoring issues resolved vs. observed
Alert Management System (AMS)
The Group’s shared accident declaration and analysis database AMS, (Alert Management System) monitors lost time and generates alerts and flash reports. Upgraded in 2017, the system now offers unlimited access, global information sharing and simplified reports.
Golden Safety Rules
In 2016, Nexans defined 15 Safety Golden Rules based on the main risks and most serious or common types of accidents. Each quarter, the Group measures and analyzes its overall compliance and defines corrective measures – at the end of 2017, overall compliance had reached 95%.
Safety Day
Since 2014, Nexans has held an annual Safety Day at all its sites - using a shared format and a variety of activities focusing on workplace health and safety – to set safety goals and share best practices.
Behaviour Based Safety
To further boost its safety performance, the Group is now developing a BBS, or Behavior-Based Safety, program. A train-the-trainer session took place at the Cortaillod site in Switzerland in September 2017, representing the official launch of this program initially developed in Sweden to enable each employee to change habits based on mutual encouragement.
Communicating about behavior contributes to improving workplace safety performance. BBS methodology mainly involves practical exercises performed in workshops with HSE experts. They become real teachers who will then be responsible for developing this culture throughout their own sites.
Workplace health
The main prevention measures cover risks involving manual handling, cable drums and/or strenuous movements and extrusion processes. Entities identify and monitor possible occupational illnesses according to their local legislation.
Currently these figures are not consolidated at the Group level.
Given our activity, the following may be identified as occupational illnesses: musculoskeletal disorders, hearing problems and exposure of employees to chemical risks. Some sites have started offering special workstation ergonomics awareness training sessions as well as regular check-ups for staff to monitor for musculoskeletal, cardiovascular and psychosocial issues. Other safety measures include the systematic use of personal protective equipment when risk assessments require it in certain site areas or workstations.
In addition to regular health check-ups, employees were surveyed to assess their stress level, exposure to noise pollution and hazardous substances, workstation ergonomics, etc., to prevent health
Along with its measures to reduce the risks of damage to employee health or loss of capacity to work, Nexans also takes local initiatives to support health education and public health programs. These programs encourage employees to adopt healthy behavior on a day-to-day basis. They may involve:
- free health check-ups for employees in countries where access to health care is difficult or costly - in Canada, Singapore, South Korea, the United States and Morocco, Nexans provides medical exams and vaccinations;
- encouraging physical activity and exercise by making sports equipment available (fitness room, coach..)
- awareness and prevention campaigns (addictions, nutrition,cardiovascular diseases, etc.) that can be tailored to local priorities
Our websites
Select your country to find our products and solutions
-
Africa
- Africa
- Ghana
- Ivory Coast
- Morocco
- North West Africa
- Americas
- Asia
- Europe
- Oceania